3D Printing : Goat Beard & Deer Horn
Mission
To convert animal products into cruelty-free & eco-friendly replicas, using bio-degradable 3D printing processes.
Problem space
Traditional German garb is still popular today thanks to Biergarten, Maypole and Christmas festivities. However, the accompanying accessories are produced from animal products and use wasteful methods. How might we leverage 3D printing to create cruelty-free, environmentally-friendly replicas of deer horn and goat beard?
*Produced as a final project for critical making class.
Tools
Rhinoceros
Cura
Ultimaker 3 printer
Sewing machine
PLA Filament (Biodegradable)
Meshmixer
Woolen felt
Acrylic Paints
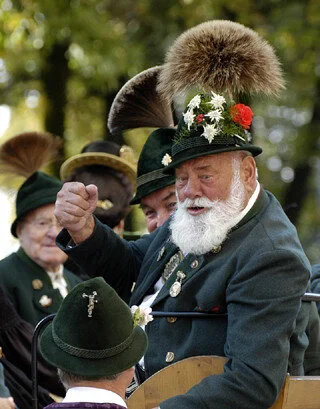
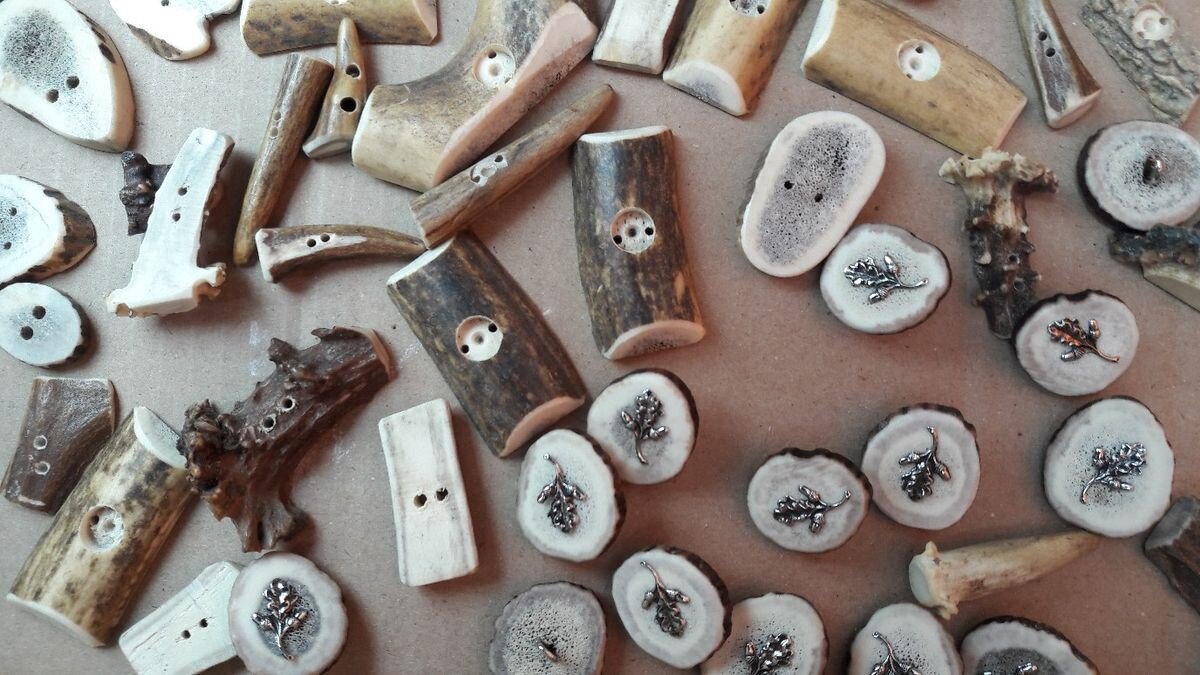


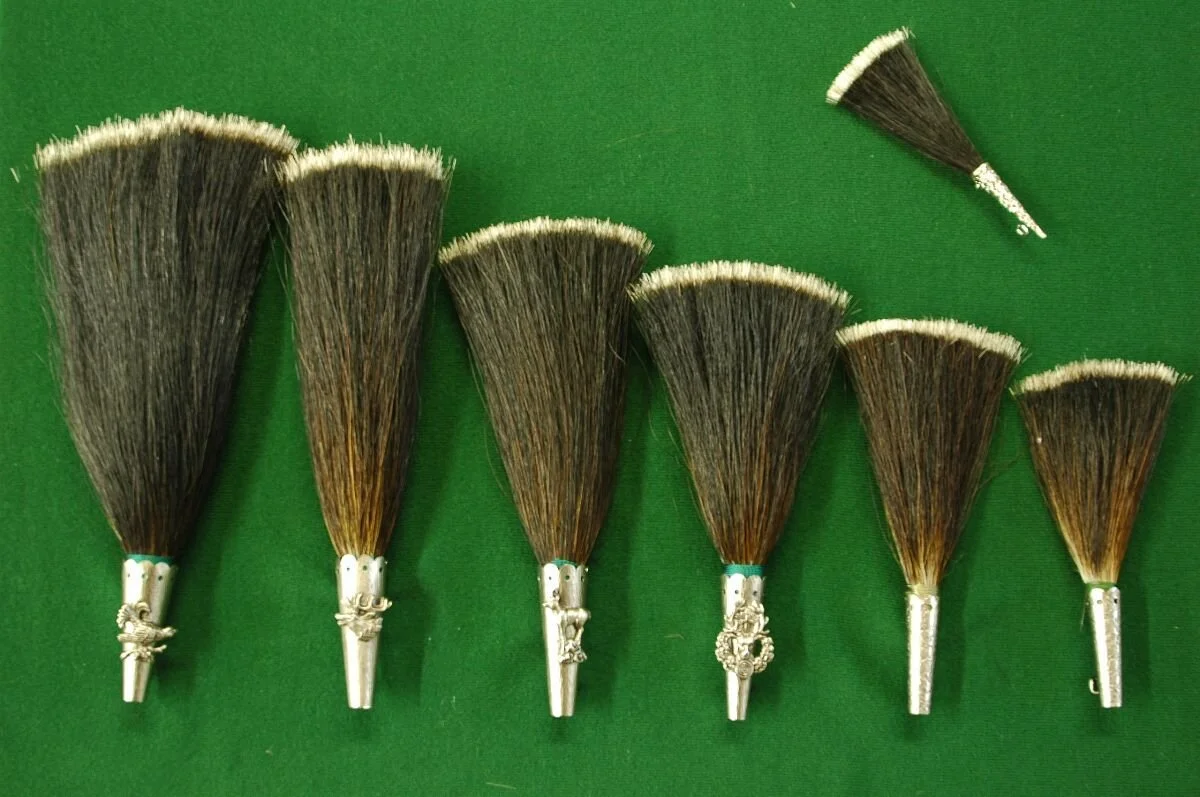

Observations
Reproducing traditional German accessories with 3D printing processes creates a unique and interesting opportunity to touch, hold and feel each object. The printed objects inspire a greater appreciation for the attention to detail and precision required to design objects true to their natural form.
Projected Impact
With traditional garb still a popular trend amongst Germans of all ages and races, the need for animal products remains steady. If, however, eco-fashion takes root within traditional clothing manufacturing, the industry could effectively eliminate animal-cruelty and replace goat beard and deer horn with biodegradable, 3D printed replicas. These are easy, cheap and fast to produce, while their impact would be immense.

“In Munich alone, 6.3 million people visit the Oktoberfest annually - add to that 8000 employees. Most everyone is in traditional garb.”
-Deutsche Post, 2018
Printing Deer Horn Buttons
This example is typical of simple deer horn buttons. The top-most layer preserves the original texture of the deer horn; whereas the inner circle is carved out and smooth.
Starting from scratch, I modeled the buttons in Rhino (a CAD 3D modeling software). To mimic the authenticity of the buttons’ texture and form, each was uniform in size but unique in texture.
This example is typical of a men’s felt vest. In fact, both the vest and the red checked shirt feature deer horn buttons.
After printing the buttons, I used acrylic paint from the dollar store to reproduce the colors of deer horn. Then I sewed button holes onto loden- or traditional shrunken wool typical for a vest.

Printing a Pewter Hat-Pin
In this example, a pewter hat-pin is embellished with an edelweiss flower, a typical symbol in Southern Germany and Austria.
To re-produce the pin in Rhino, I modeled a conical shape. Next, I built an Edelweiss flower and mounted it onto the pin.

I printed several iterations at various fidelities and settled on a thinner, simpler model.
These initial prints revealed several pain points: too thick, too heavy, too rough, and the flower broke off.
Printing Goat Beard
In this example, a women is wearing a goat beard hat pin. The beard fans outward and has darker tips.
To model the same beard, I built a pine tree-like structure. Each “branch” was planted along the truck in a circular fashion, reaching outward. To keep the strands of hair straight, I relied on a “sacrificial wall” to support each individual one.
After printing, I severed the strands from the wall with an electric heated exacto knife.
Each print took roughly 2.5 hours to complete.

Final product
To achieve the shape of the hair, I used the heat of a blow dryer to mould the strands upwards. Lastly, I painted the “hair” to mimic the colors of a goat’s beard.
These accessories were printed using PLA filament- a biodegradable material made of cornstarch. PLA greatly reduces environmentally harmful waste in the printing process.
This project solved for my initial goals : the hat-pin and the buttons are both environmentally friendly and cruelty-free.
All files available on Github https://github.com/ydanyluck